the new standard of
rotational molding
GVL Poly molds without compromise.
At GVL Poly, this isn’t just manufacturing—it’s craftsmanship backed by SMART® technology, real collaboration, and an obsession with getting it right the first time.
From precision-engineered molds to zero-return quality control, our SMART® technology delivers parts that fit, perform, and endure. Every piece is personalized by expert hands, not pumped out on autopilot. We don’t chase cheap—we create better. Because when you care more, the product shows it.
THE GVL Poly DIFFERENCE
SMART MOLDING TECHNOLOGY
Our advanced SMART molding process reduces material waste, cuts energy usage, and ensures perfect parts—right from the start.
PROCESS design OPTImization
Our expert engineers collaborate directly with you to create custom solutions tailored to your exact needs—because this isn’t just plastic, it’s personal.
zero returns zero compromises
With precise temperature control and finish refinement, we create parts with superior cosmetic surface finish.
inventory you can count on
Through JIT, Kanban, and managed inventory systems, we scale with your demand—so your parts are where you need them, when you need them.
THE FUTURE OF rotational molding
SMART® MOLDING TECHNOLOGY
Up to 10% less raw material
15% lower energy use
Shorter lead times
Superior part consistency
FINISHED PRODUCTS
INDUSTRIES WE SERVE
AGRICULTURE
Durable, precision-molded components for OEMs and aftermarket applications—engineered to withstand the toughest environments.
MEDICAL & HEALTHCARE
Clean, consistent, and tightly controlled production for high-performance components—where quality is non-negotiable.
INDUSTRIAL EQUIPMENT
Custom solutions for complex, heavy-duty applications—designed for longevity, fit, and seamless integration into your systems.
SPORTS & RECREATION
Parts that hold up under pressure. From vibration to impact, our products move with strength and stability.
CONSUMER PRODUCTS
High-quality, brand-consistent plastic parts that combine form, function, and flawless finishes.
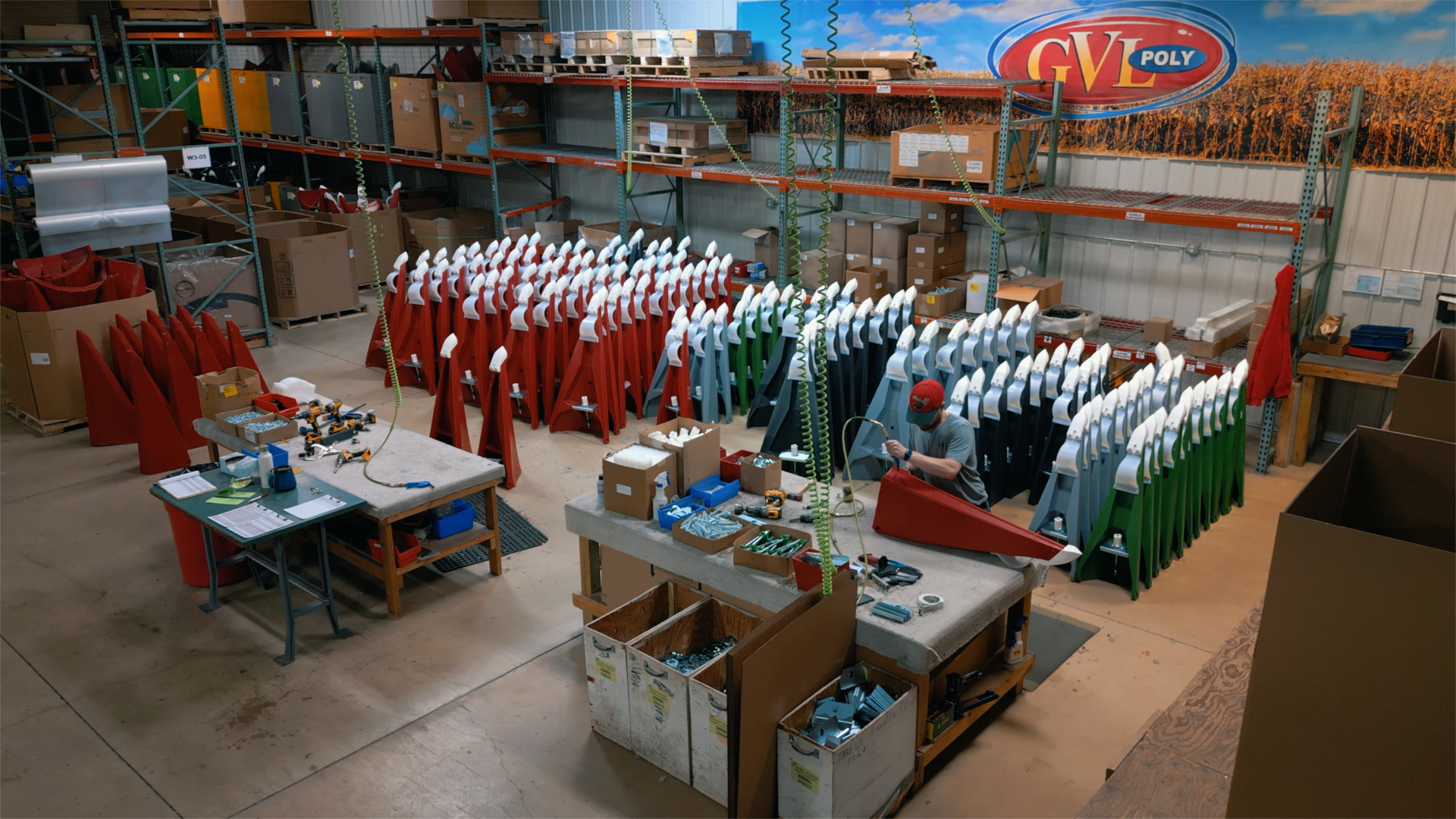
want to WORK TOGETHER?
WE CAN’T WAIT TO HEAR FROM YOU.
learn MORE About GVL Poly
-
who we are
-
what we do
-
who we serve
-
contact